“I need a label that can withstand a rough supply chain environment, but I also need one that won’t fade. What’s the best choice?”
This is a question we hear often at SmartShield. When it comes to industrial label printing, the choice between thermal transfer and direct thermal printing isn’t always obvious.
Thermal transfer and direct thermal printing are two of the most common label printing methods used in industries such as defense, aerospace, and medical. But how do you choose the right one? Both offer high-quality barcode and text printing, but the right choice depends on factors like durability, cost, and printing flexibility. This guide will help you compare thermal transfer vs. direct thermal printing to determine the best fit for your business.
Here are five key factors to consider.
1. Thermal Print Head Lifespan
One of the most significant differences between direct thermal and thermal transfer printing lies in the lifespan of the print head.
With direct thermal printing, the print head comes into direct contact with the label material. This friction, combined with any dust or debris, wears down the print head faster, leading to more frequent maintenance and replacements.
Thermal transfer printing, on the other hand, uses a ribbon between the print head and the label material. This ribbon acts as a buffer, protecting the print head from wear and tear and prolonging its life. The ribbon’s coating also helps reduce static and friction, giving thermal transfer printers a clear edge when it comes to durability. For industries like aerospace and medical where precision and reliability are key, the reduced maintenance of thermal transfer printing is a major plus.
In short, if long print head life is important for your operations, especially in environments prone to dust and debris, thermal transfer is your better option.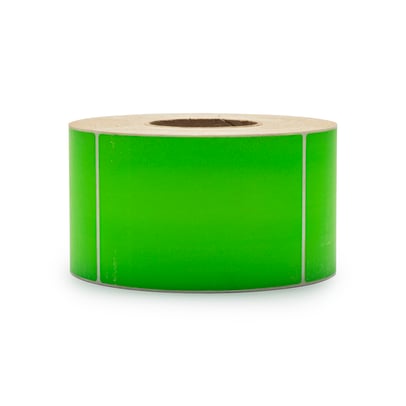
2. Flexibility in Printer Configuration
One advantage of thermal transfer printers is their flexibility. They can be configured to print using either a ribbon (thermal transfer) or without one (direct thermal). This gives you the freedom to switch between methods based on your specific needs—whether you're printing durable, long-lasting labels for defense projects or quick, temporary labels for electronics packaging.
Direct thermal printers, by comparison, are typically simpler and cost less because they don’t require the hardware for handling ribbons. However, they lack the flexibility to print in both modes.
For companies that need versatility in their printing processes, thermal transfer offers more options, though at a slightly higher initial cost.
3. Choice of Printing Media and Costs
Your choice of printing media plays a critical role in determining both cost and label quality. In direct thermal printing, the print head directly contacts the label material. If the material is abrasive, it can wear down the print head more quickly, resulting in higher maintenance costs. Thermal transfer printing avoids this issue, as the ribbon acts as a protective layer, meaning less direct abrasion on the print head.
While direct thermal labels tend to be more expensive due to their specialized coating, eliminating the need for a ribbon can sometimes reduce overall costs—though this isn’t always the case. For example, in defense and medical applications where durability is key, the added lifespan of thermal transfer labels and the print head often outweighs the small cost difference.
4. Label Lifespan Requirements
When choosing between thermal transfer and direct thermal printing, the intended lifespan of your labels is a critical factor.
If your labels need to survive long-term exposure to harsh conditions, such as heat, sunlight, or chemicals, thermal transfer is the clear choice. Labels printed with this method are much more resistant to wear and tear and can last significantly longer. This is crucial for applications in industries like aerospace, where equipment can be exposed to extreme environments, or medical, where labels need to stay legible for the life of the product.
On the other hand, if you’re printing labels for items with a shorter shelf life—for example, in robotics or electronics packaging, where the products won’t be exposed to harsh conditions—direct thermal printing may be sufficient. Just bear in mind that these labels are prone to fading over time and may not be suitable for long-term storage.
5. Environmental Impact
For companies focused on reducing their carbon footprint, it’s worth noting that thermal transfer ribbons are made using poly-based materials derived from crude oil. This adds an extra layer of waste that direct thermal printing avoids, as no ribbon is required.
That said, the environmental benefits of direct thermal printing are limited by the method’s shorter label lifespan and higher maintenance needs. In some cases, the extra sustainability benefits of using long-lasting labels from a thermal transfer printer may outweigh the waste of ribbon use.
At SmartShield, we’re always following the latest advancements in printing technology. We expect that direct thermal technology will continue to improve in durability, but for now, thermal transfer remains the more robust choice for industries where long-lasting labels are critical. Read more about our direct thermal and thermal transfer labels.
Which Method is Right for You?
Ultimately, the choice between thermal transfer and direct thermal printing comes down to your specific needs. In industries such as defense, aerospace, medical, robotics, and electronics, where durability, precision, and reliability are critical, thermal transfer is often the best option. However, if you’re looking for a cost-effective solution for short-term labeling, direct thermal printing may fit the bill.
Ready to elevate your business processes?
At SmartShield, we help you find the right printing solution tailored to your needs. Contact us today, and let’s explore how we can streamline your labeling process and improve your bottom line.
Reach out today for expert guidance on choosing the right static protection foam for your components.