When it comes to clinical equipment, medical packaging isn’t just about protection - it’s about precision, compliance, and reliability.
A leading medical manufacturer came to us with a challenge: they needed a plastic case to house their delicate device, but before it could be put to use, the packaging had to pass strict certification tests.
One requirement stood out - during a drop test, the unit could experience no more than 10G’s of force.
After working with multiple packaging providers who couldn’t meet this target, they turned to SmartShield for a solution.
Here’s how we helped them achieve what others couldn’t.
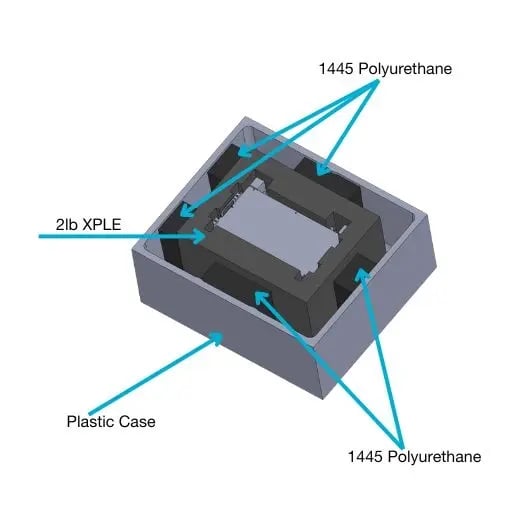
The SmartShield Solution: A Dual-Layer Foam Suspension System
To solve this problem, we engineered a customized foam cushioning system that absorbed shock while keeping the device secure. This included two components as follows:
- Primary Protection: We packed the medical unit in a 2lb density foam, offering a firm but protective enclosure
- Suspension Layer: We then reinforced the foam set with a low-density polyurethane foam, which acted like a suspension system—absorbing and dissipating impact energy during drops.
This innovative dual-layer foam design successfully reduced impact forces to meet the required 10G limit, ensuring the medical device was fully protected.
The Result: Medical Packaging Certified and Ready for Use
Thanks to SmartShield’s precision-engineered medical equipment packaging, the customer achieved certification compliance and could confidently move forward with their product. Where other providers had failed, our expertise in protective foam engineering provided the breakthrough solution they needed. That’s the SmartShield way!
Need help with a custom-engineered medical packaging solution?
Give us a call and speak to one of our friendly expert team